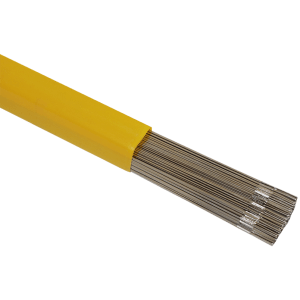
101070/A
TIG WELDING WIRE (STAINLESS STEEL)
In Stock CPT
Web price
R 328.57 / KG
R 328.57 / KG
R 285.71 ex vat
Apply now for bulk pricing
Free delivery on orders over R1500
TIG WELDING WIRE (STAINLESS STEEL)
In Stock CPT
TIG WELDING WIRE (STAINLESS STEEL)
In Stock CPT
Notice
We and selected third parties use cookies or similar technologies for technical purposes. We may use information on a device and process personal data like your usage data for the following advertising purposes: personalised advertising and content, advertising and content measurement, audience research and services development. If you give consent, it will be valid only in this domain. Denying consent may make related features unavailable. Use the “Accept” button to consent. Use the “Reject” button to continue without accepting.